5S method
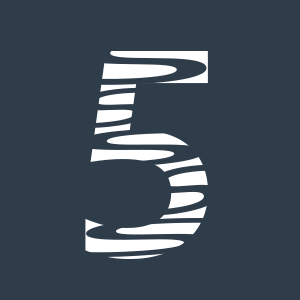
A principle formalized by Toyota to improve the organisation of a workspace.
We can associate each S with an action: Sort, Set (in order), Shine (Clean), Sustain, Standardise
1. keep only what is useful 2. tidy up according to your use 3. have a clean environment 4. maintain good working conditions 5. involve people
The 5S: origin and definition
It was in the 1980s, during the golden age of Japanese industry, that the world discovered this method. Although it was in Japan that it was formalized, its origin is American: 5S was born out of TWI: “Training Within Industry”, a programme set up by the USA during the Second World War, taken over by Japan at the time of its reconstruction. Please find below a summary table that will allow you to understand each notion:Japanese expression | Associated actions | Finality |
---|---|---|
Seiri | Sort | Removing the unnecessary, bringing the useful closer |
Seiton | Set in order | Optimizing storage |
Seiso | Clean | Working in a clean environment |
Seiketsu | Sustain | Keeping order |
Shitsuke | Formalize and Involve | Transmit good practice and involve those concerned |
- Specifically suited to a production workshop
- On your own desk
- Your teenager could use it as inspiration for tidying up his or her room… but there are insurmountable cultural guards in place.
1ᵉʳ S: Seiri / Sort – “Get rid of useless”
This first stage consists of sorting, with a leitmotiv: something frequently used must be within reach, move away what is rarely requested.
This principle can be graduated by frequency of use and distance.Use | Distance to user |
---|---|
Continue | As close as possible to the user (even on the user) |
Daily | Always at hand (on the desk, on the workbench…) |
Weekly | Stored in the area of use (the workstation, the room…) |
Monthly | Stored in the service/building |
Annual | Archived away (basement, remote building) |
We wonder… | why we keep this, let’s get rid of this? |
2ᵈ S: Seiton / Set in order – “A place for everything and everything in its place”
Now that everything is roughly grouped by area we need to make a relevant arrangement, based on common sense rules:
- Categorization : alphabetical, by topic, by application…
- Security : don’t store the chainsaw balanced on a corner of a shelf
- Consider the flow and process: components are arranged in order of use
- Standardisation: if a tidying is optimized then it might as well be applied in other comparable cases
- Accessibility: one must easily find and reach what one is looking for.
3ᵉ S: Seiso / Clean – “The big spring clean”
Nothing complicated with this point, the goal is to start a task in a clean environment and to conclude it in the same way.
There is a real need to emphasize the systematic approach:- Restore the work area to its prior state each time a task is completed
- Deep cleaning periodically (at the end of the day, week, activity cycle…)
4ᵉ S: Seiketsu / Sustain- “Over the long-term”
All the effort put into implementing the first 3 S’s has produced a working environment best suited to your context. This deserves to be sustained over time.
We have seen the importance of maintaining a clean environment, it is equally important to sort and tidy at all times, in order to maintain an efficient work, in the best conditions. This will save you time, and spare you the well-known “annual rush” of the big clean-up, which takes up precious time and whose benefits are quickly diluted over time. There are two complementary approaches:- Continuous approach: you keep the environment clean and tidy on a daily basis.
- Events approach: with each change in the organisation, it is important to take a “5S look”
5ᵉ: Shitsuke / Formalize and involve: “I have a dream”
The 5S approach must be adopted by all stakeholders, the following points should be noted:
- First of all, it is necessary to make involved people aware of this approach, to explain its purpose, means, methods, responsibilities…
- Formalizing helps a lot: in the form of a documented procedure, a table or drawing / poster.
- Involve staff, ask their opinion, encourage initiative
Consequences and contributions
A few points that should definitely convince you of the value of the 5S approach:- You can expect to improve your productivity
- The security of operations is likely to increase
- The satisfaction of people can only be increased in a welcoming environment
- Your customers and other subcontractors, and even auditors, will have a positive a priori of your business at the mere sight of your organisation
Illustration: The 5s method
Find the 5S method illustrated in an infographic, which uses the illustrations from the article, it will blend harmoniously with any type of interior (click to access the A4 version):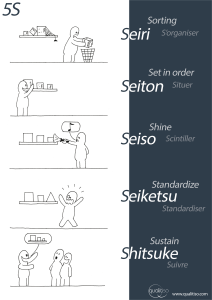